Hard Coating
PVD hard coatings produced by INOVAP have the distinction
of a wispy multi layer structure.
The coatings were deposited by the PulsArc treatment.
This process is a newly developed PVD technology with a multiplied electron emission and ionized plasma density on substrate surface caused by a controlled high current pulses.
Thus the
deposited coatings have an improved wear-resistance and a reduced surface roughness.
Hard coatings like TiN, TiAlN, TiCN und CrN have the
destinction of following properties:
•
|
The tough hardness decreases abrasion and the free formed
surface and the scour wear
of drillers, millings and hobs.
|
•
|
Hard coatings decrease
the inclinations of tools to
agglutinate or to weld with
workpieces and beware cutting edges and function
surface from agglomerates and agglutinations.
|
•
|
Decreased friction between the hard coated tools and workpieces
reduces substantially cutting and forming forces.
|
•
|
The hard coatings
are chemically resistant and low reactive for a longer tool life time.
|
•
|
The strong adhesion on tool surfaces and quasi-elastic behaivor of hard coatings reduce spallings, ruptures and outbursts also during strong forming and great cutting forces.
|
Tools with hard
coated surfaces allow a substantial longer life time and a better usage rate for machinery. One can apply
higher processing speed and gets
more precise processed surfaces. It includes a reduction of setting-up and alignment time.
|
The calotte grindings
are closely to each other
in rows on measurement surface and can
be found and measured with a microscope very easily.
Grinding parameters (rotating speed, number of rotations for each single
calotte, distance between calottes on surface) can be selected and
controlled by a SPS-unit.
Afterwards the unit also calculates the thickness and final depth.
For layer thickness evaluation the very best
or an average value of several
calottes can be selected.
That implies thickness measurent values of high reliability and low standard
deviation. The KSG 110 is
very applicative because of its
robustness also in production
fields.
It is also possible to measure
the wear coefficient as a function of depth
reached in the coating. Even very small calotte grindings can easily be found
because of its placement in rows.
|
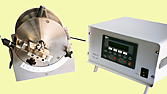
Technical data
•
|
Adjustable force FN: 0 - 0,32 N (steel ball 20 oder 30 mm); 0 - 0,63 N (WC-ball 20 mm)
|
•
|
Tilting angle 0 - 90°
|
•
|
number of revolutions
50-5000 min-1
|
•
|
Rotations: up to
1000000 / grinding
|
•
|
Grindings per sample: 10
|
•
|
Shown results: thickness
of coating and depth of
grinding in µm
|
•
|
Calculation: wear volume
in mm3; wear coefficient
in m3/Nm
|
|